See how factories using Autonomous Ground Vehicles can benefit from advanced wireless networks to increase efficiency and safety, and reduce dead-spots and bottlenecks.
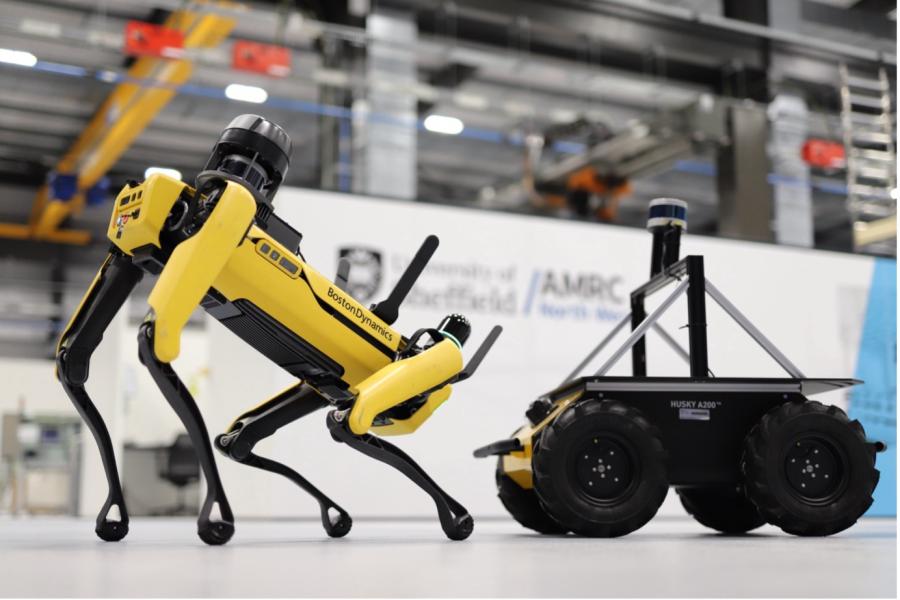
What is the problem to be solved?
Autonomous Ground Vehicles (AGVs) and Autonomous Mobile Robots (AMRs) are an important part of many modern manufacturing facilities. Their goal is to automate the transportation of parts between manufacturing areas in complex environments seamlessly, integrating with other technologies for more effective automation and management of processes. Involved parties include telecoms operators, robot manufacturers, and system integrators. They aim to achieve reliable communication to control AGVs in real-time, even in remote or complex areas within the facility. Additionally, they aim to ensure the secure exchange of large quantities of data in a short timeframe with AGVs, integrating with advanced sensing technology for increased autonomy and safety.
However, AGVs and AMRs often encounter connectivity issues, with Omron citing that 90% of all AGV faults are connectivity related. These vehicles operate in large, potentially hostile environments sometimes filled with dust, radiation, and other potential hazards, which can be detrimental to their wireless connections. Such environments also tend to be highly metallic, causing further disruptions.
What is the solution to the problem?
The implementation of AGVs and AMRs across production and logistics operations requires a stable communications network. This network must manage the simultaneous operation of multiple AGVs and provide the necessary coverage and performance to ensure control is maintained as the vehicles transition between different environments. 5G mobile networks are eminently suitable for this and can also be used to facilitate high bandwidth video feeds, enhancing real-time monitoring and control. Network options, which can include Wi-Fi 5/6, private/public/hybrid 5G, largely depend on the application, environment complexity, and required security levels. Roaming between private and public networks can also be made seamless with 5G technology if required. Although this is doable in theory this is a complex technical challenge at the moment.
Commercial model (Business Case)
Implementing AGVs controlled via a 5G network can significantly transform manufacturing operations. These AGVs can replace forklift drivers, trolleys, and line following robots, leading to a substantial increase in efficiency and a reduction in labour costs. The use of AGVs in remote, hostile environments, as demonstrated in various case studies on the UKTIN website, can not only replace manual tasks but also reduce associated paperwork and delays. This transition can increase productivity by up to 30% and reduce labour costs by as much as 40%.
In addition, the use of AGVs can reduce downtime and IT support tickets, further enhancing efficiency. The integration of AI with factory automation can increase production by 33% per hour, reduce defect rates by 88%, and reduce assembly-line staff by 50%. Moreover, precision monitoring and control over a P5G network can improve machine productivity by 15% and reduce average defect rates by 10%.
While the initial investment in 5G Networks for AGVs might seem substantial, the payback period, based on salary substitution and efficiency gains, can make a compelling business case. Furthermore, the use of AGVs allows for 24/7 operation, eliminating low skilled repetitive work and reducing the risk of injuries, both increasing efficiency and reducing health & safety incidents.
Benefits
Integrating AGVs into factory operations via a 5G network can offer a multitude of benefits. Firstly, the use of reliable robots with fast data transfer capabilities can significantly improve productivity and efficiency. These robots can operate on continuous shifts, reducing the constraints imposed by human work schedules, and enabling a 24/7 operation.
Secondly, the use of AGVs can centralise coordination of robots, allowing for smoother navigation and reduced downtime. The robots' extended range enables them to navigate across different environments, including indoor and outdoor production and logistics points. This feature reduces the risks of mishaps due to human error such as tiredness or carelessness. Additionally, centralisation and long-distance coverage allows for remote tele-operation and control of AGVs, which can reduce costs and improve efficiency.
Lessons Learnt
Deploying AGVs in a factory environment requires careful planning and coordination among various stakeholders. Given that AGVs are expected to co-exist with human workers, ensuring safety and addressing concerns around 5G emissions and machine operations is crucial. Early engagement with the workforce to communicate these safety measures and benefits can help in smooth implementation.
A lack of radio coverage can lead to blind spots, delays, and traffic jams in AGVs. Therefore, thorough planning of the physical path and wireless network design, including quality of service and interference, is essential. Undertake rigorous testing during initial trials before making substantial investments.
Consider potential commercial and project pitfalls, including insufficient scope of work, excessive customisation of design, and integration challenges. Have a clear line of communication between AGV technical support and the user.
If you’re ready to embark on a connectivity project, we can point you to the suppliers with expertise in your sector.