This case study explains the role of wireless communication between marine fish farms and land-based hubs, the specific challenges encountered at sea and the digital solutions offered by resilient communications specialist, Krucial Ltd (https://www.krucial.com/).
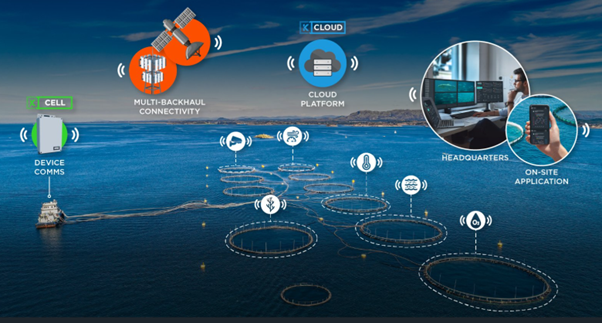
Figure 1 - Remote monitoring for aquaculture systems with Connected Seafarm (source, Krucial Ltd).
What is the problem to be solved?
This case study is aimed at marine aquaculture producers who can benefit from remote data collection from distant or inaccessible farm locations. The purpose is to improve operational efficiency and safety, and to mitigate against adverse events. The case study applies particularly to marine fish farms, where underwater sensors and video cameras add value via remote monitoring of livestock behaviour and of environmental conditions.
What is the solution to the problem?
The technical solution described in this case study is an end-to-end service designed for the Aquaculture sector, particularly suited to offshore operations, built on top of Krucial’s resilient, off-grid capable, hybrid cellular/satellite data infrastructure. An overview of the Connected Seafarm’s core infrastructure can be found here: https://www.krucial.com/krucial-connect.
Commercial model (Business Case)
Krucial’s commercial services to the aquaculture sector have continued improving since first launching in 2022. Originally offered with a limited number of monitored parameters, the Connected Seafarm has grown in response to feedback from the sector to offer a range of services to support farming operations.
To date, the salmon farming sector has exhibited preference for OpEx contracts (in contrast to some other marine industries). Service contracts are typically 36-48 months in duration, with hardware, communications, storage and cloud access charges all rolled into a simple single price paid regularly for the duration of a contract.
For salmon producers, the business case for adopting Krucial’s Connected Seafarm is to unlock the benefits of autonomous monitoring and remote control for their operations, even on the most remote and challenging farm sites. While Connected Seafarm’s benefits stand out most uniquely on sites where no other technology has been able to operate reliably, the ability to deploy a consistent monitoring capability across all sites is advantageous regardless of operating environment.
Benefits
The key benefits of adopting Krucial’s Connected Seafarm is delivery of a dependable platform, on which resilient, scalable and massively value adding solutions can be built. This value of digitisation in aquaculture today is primarily operational, which means that picking the correct technology on top of which to anchor operations is fundamental to the continued success of an organisation.
The flexibility of the Krucial offering, and the ability to use it not just for environmental monitoring but also remote feeding and remote control of site operations means that the platform has a direct positive impact on the crucially important feature of fish feeding efficiency.
Better data-drive decision-making is a key driver of the transition towards precision fish-farming, where resources and costs are optimised, stock performance is at its maximum, and sustainability is enhanced.
Lessons Learnt
Key lessons learned by Krucial in developing and implementing digital aquaculture monitoring & control solutions are:
Choosing open collaborative architectures over closed-source systems helps businesses avoid industry lock-in, enabling greater flexibility and innovation. Open systems allow seamless integration, scalability, and adaptability, while closed-source solutions can restrict growth and increase dependency on a single vendor. Embracing open technology fosters long-term success by ensuring compatibility with future advancements and reducing costly limitations.
Once technology becomes essential for operations, it must function reliably. Making it crucial to have fallback options in place and systems must have built in redundancy measures.
Aquaculture farms vary in size, location, and operational requirements, meaning their digital infrastructure must be both adaptable and scalable to meet these diverse needs. Factors such as environmental conditions, species farmed, and regulatory requirements can all influence the type of technology needed. A flexible digital solution ensures that farms can integrate new technologies, scale operations efficiently, and adapt to changing conditions without significant overhauls. By prioritizing adaptability, aquaculture businesses can optimize productivity, enhance sustainability, and future-proof their operations against evolving industry demands.
Digital adoption in aquaculture varies, but the industry is steadily moving toward greater integration. Growing demand for sustainability, regulatory pressures, and efficiency are driving this shift. As technology becomes more accessible and cost-effective, even hesitant operators are likely to adopt digital solutions to stay competitive.
Technology that adds value to the salmon industry has the potential to benefit other finfish and non-finfish aquaculture sectors, as they often operate in the same marine environments and face similar challenges. Issues such as water quality monitoring, disease prevention, and sustainable feed management are common across different types of aquaculture. Innovations in real-time data collection, automation, and predictive analytics developed for salmon farming can be adapted to improve efficiency, sustainability, and profitability in other sectors. By leveraging shared solutions, the broader aquaculture industry can accelerate technological progress and enhance overall resilience in the face of environmental and economic pressures.
The rapid advancements in AI, machine learning, and other emerging technologies are driving exciting developments across various industries, including aquaculture. As these innovations continue to evolve, businesses must ensure that any technology investments made today are future-proof. This means selecting solutions that are scalable, adaptable, and capable of
integrating with new advancements as they emerge. Future-proofing technology helps businesses stay competitive, avoid costly system overhauls, and maximize long-term value. By prioritizing flexibility and forward compatibility, companies can ensure they are well-positioned to leverage the full potential of digital transformation in the years to come.
If you’re ready to embark on a connectivity project, we can point you to the suppliers with expertise in your sector.