Methane emissions from farms contribute to global warming but can be used as fuel for heavy off-highway vehicles which it would be impractical to electrify.
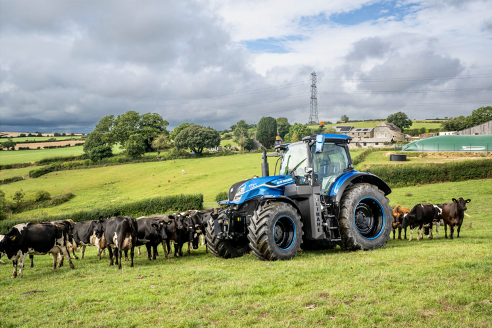
What is the problem to be solved?
Farmers and growers are being challenged by consumers, supermarkets and Government to reduce greenhouse gas emissions from primary production. There are challenges for all agricultural sectors who rely on large tractors to carry out a range of tasks. These vary widely from heavy field cultivation requiring maximum draught at low speed to higher speed field tasks such as mowing implements that take power directly from the tractor. These tasks are very seasonal and must be completed when weather and ground conditions allow. Weather windows can be quite short, and the business case for large, capable machinery is based on the ability to get seasonally critical tasks accomplished before the weather closes in. Missing key planting dates can be very damaging to farm income.
Modern tractors deliver all this capability along with the ability to carry out on-highway transport tasks and it is easy to appreciate that the “mission profiles” for each of these tasks is massively varied in terms of speed, power, carrying capacity, draught loading and duty cycle. In consequence, fuel demand fluctuates significantly, and machines need to refuel in different locations, sometimes in remote field situations.
Electrification is one option for smaller tractors, but for larger tractors, this is impractical because of the weight of the battery that would be needed (you quickly end up with no carrying capacity left on the tractor) and the kind of grid connection that would be needed to recharge a very large battery in a reasonable time.
What is the solution to the problem?
In this use case, reliable service and the coverage of connectivity is much more important than outright speed and latency. Any disconnections in mobile communication are likely to result in a fall in pipeline operating efficiency, but does not compromise safety. Ultimately, down-time for the tractor has significant economic consequences. In farming it is not just the value of the operator’s time that is lost, it is the lost opportunity of achieving crop establishment, harvesting or some other time critical task before the weather closes in.
Whilst high reliability and ubiquitous coverage are preferred and should be maximised, there is not a need for resilience in the form of secondary / alternative routing for backhaul etc.
Latency, is also not an issue in this use case – slightly delayed data is not a significant issue.
However, the user interface for the tractor operator and the methane pipeline operator needs to be well designed and much of its attraction will be the real time nature of the information displayed.
Commercial model (Business Case)
The big drivers of on-farm adoption of liquid fugitive methane (LFM) will be:
- Policy incentives (as part of the transition away from Area Payments to more environmentally sustainable technology).
- The farm business making a demonstrable environmental commitment (useful for gaining/maintaining supply contracts). The system will need to interface with existing carbon credit tools on the market to ensure this is auditable.
- Reduced fuel costs (diesel is a significant cost to farms and is subject to market volatility).
- Energy self-sufficiency (the ability to control one’s own cost of energy production). On average, a dairy farm with 50 cows is generating enough accessible fugitive methane to power one tractor.
- Potential to sell surplus methane to other farms or use it to generate electricity (stackable use case with grid demand planning and EV charging maps).
- Confidence in a virtual pipeline being able to supply fuel on a just in time basis with no unscheduled down-time.
Benefits
The benefits of such a system are clear. Firstly, the significant reduction in CO2 emissions, with the prospect of carbon negativity for some dairy farms because methane is removed at source (methane is much worse than CO2 as a greenhouse gas). Supplier relationships are strengthened, because brands are all concerned to improve their environmental credentials. Carbon reductions need to be auditable, and systems need to integrate with existing carbon credit tools (which will also require mobile connectivity).
Demand planning is a critical function of an effective virtual pipeline, and this will be dependent on good connectivity. Undetected spikes in workload could create unexpected downtime if a tractor runs out of fuel sooner than expected. Any tractor down time is likely to have a much larger cost that simply the operator’s time. All of these benefits depend on reliable telecoms.
Lessons Learnt
Do:
- Consider who the right connectivity partner is for the local communication solution.
- Undertake a connectivity coverage assessment for all parts of the farm.
- Refine demand forecasting to drive pipeline efficiency.
- Learn from previous challenges: understand previous unexpected demand events.
- Focus on system resilience in case of network issues.
Don’t:
- Think about the solution in isolation - consider who the beneficiaries are (and therefore who pays for the connectivity), and what other data could be collected at the same time.
- Forget the training requirements for support technicians to support this effectively in the field.
- Forget costs of network licensing/upgrades/repair.
If you’re ready to embark on a connectivity project, we can point you to the suppliers with expertise in your sector.