See how advanced networking options can be exploited to provide connectivity across a whole site, enabling a smart factory and reducing maintenance overheads.
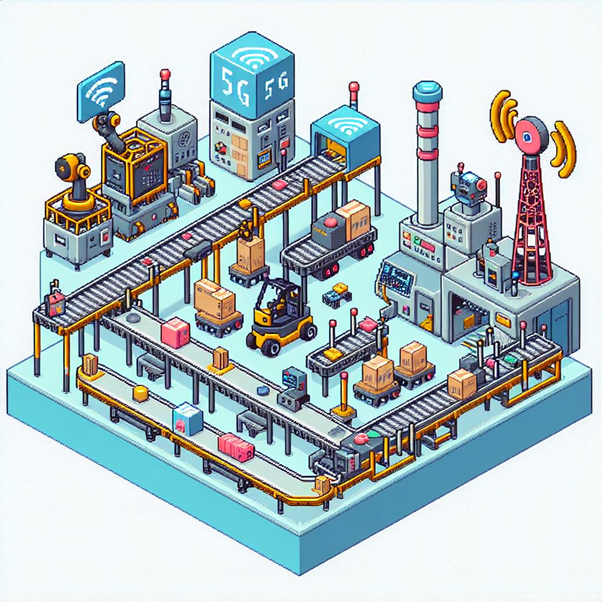
What is the problem to be solved?
In today’s digital age, data connectivity is crucial for the efficient operation of manufacturing companies. However, many organisations struggle to reliably support the sheer number and variety of different digital endpoints that are deployed as there is no “golden bullet” when it comes to connectivity, especially when dealing with older factory buildings and sites with outdoor spaces. Some examples of the challenges faced include:
Sensorisation: Deploying sensors to monitor process variables, environmental conditions etc. can quickly turn into hundreds or thousands of devices that need to have connectivity and be managed and maintained. These can have wildly different latency, bandwidth and power requirements lending themselves to a diverse range of suitable solutions.
Inter-Site Communications: Multi-site organisations struggle to interconnect their assets and bring them all under a single physical data network. They can’t rely on Wi-Fi for all comms, and there are many scenarios where sending traffic over the internet isn’t appropriate for security or latency reasons, but the costs of dedicated dark-fibre connections are prohibitive. Therefore, there exists a need to setup a sophisticated infrastructure that can support internal and cross-site interconnectivity
Advanced Machinery and Connectivity: Modern advanced machinery such as those used in additive manufacturing require extensive wiring for connectivity across a factory. This can be streamlined using wireless technologies like 5G, which can reduce the need for physical cables and improve flexibility in machine placement and operation and reconfigurability when changes are required.
Cable Requirements for Large Sites: Large sites often need extensive cabling to support a large number of devices, e.g., CCTV, sensors and networked manufacturing equipment. This can be a significant challenge, especially in outdoor or multi-building environments where the number of endpoints and cable distances are too high
Shadow IT: This occurs when implementors set up their own equipment without proper oversight, usually because of frustrations with the IT team over perceived slow change control or unwillingness to be flexible. This can lead to security vulnerabilities and network management issues.
Safety Networks: Safety networks, such as those for fire alarms, need to be maintained and replaced more frequently to ensure reliability, and can often be difficult to access for maintenance and refresh purposes.
Tracking 'Things' in Factories: Tracking assets and materials moving around a factory can be complex and expensive, with a myriad of different technologies and no easy choices.
Interference in Manufacturing Sites: Manufacturing sites often have high levels of interference that can affect wireless networks, but they tend to do so intermittently causing dead zones or time-limited outages that can be difficult to identify and plan for.
Outdoor Connectivity: Outdoor sites often lack connectivity and rely on paper-based processes. Connectivity options can often be impractical due to power or cable-laying requirements, or difficulties in obtaining licences for wireless frequencies.
What is the solution to the problem?
Modern advanced wireless solutions such as 5G can provide excellent general-purpose connectivity options for a wide range of manufacturing and factory scenarios due to their flexibility. This can include:
Replacing Existing Connectivity Solutions with Advanced Wireless: Replacing current wired and wireless solutions with 5G, whether private or public, can significantly enhance network performance, reliability and ease-of-access. This transition can support a wide range of applications across a connected factory environment. There are now 5G-based solutions that can cover most use cases, from low-power, low-bandwidth all the way through to high-throughput for HD video.
5G as a Backup for Existing Networks: Using 5G as a backup for existing networks can provide a robust failover solution. This ensures continuous connectivity in case of primary network failures and is a particularly good ‘add-on’ use case for a 5G network that’s already deployed.
Network Slicing: Network slicing allows different users to access the same radio network in a virtually segmented manner, tailored to their specific needs and can transform a private network into something that is dynamically reconfigurable as the need arises. This capability is crucial for supporting various applications, such as giving third-parties remote access to maintain specific equipment, or segregating and prioritising control/telemetry data from regular front-office business usage.
Micro Deployments: If a manufacturing site includes outdoor space, then attaching a single external RAN to the buildings can be highly effective in covering a large geographical area ranging from hundreds of meters to a few kilometres, without needing repeaters or having to run cables away from the building.
5G Backhaul Between Different Sites: Using 5G for backhaul between different sites can extend Wi-Fi and other networks efficiently. This approach leverages 5G's high bandwidth and low latency to connect multiple locations seamlessly. This can be done privately if sites are nearby or by utilising public hybrid networks or dark fibre for longer distances.
Indoor Location Tracking: While not yet fully mature, this is a rapidly evolving area that can be another good ‘add-on’ use case if a 5G network is already deployed across a location.
Quality of Service (QoS): QoS is essential for managing network traffic and ensuring that critical applications receive the necessary bandwidth and low latency. Implementing QoS can help prioritize traffic for latency-sensitive applications, ensuring smooth operation across different networks
Commercial model (Business Case)
As previously stated, deploying a 5G network for factory connectivity is a layered approach where additional use cases build on top of each other. It may be difficult to build a business case entirely on financial grounds, but by using a combination of financial, security and extensibility arguments, a case can be made for initial deployment that then unlocks a raft of future benefits once the platform is in place.
5G networks can significantly enhance operational efficiencies through automation, real-time data analytics, and improved connectivity. This can lead to reduced downtime, optimized resource utilization, and lower maintenance costs. For example, 5G networks:
- Can significantly reduce the amount of wiring a factory requires (both for power and data transfer) which depending on the situation can save money for retrofit and green-field projects, and can contribute to reduced fire risk.
- Can completely remove the need to dig underground to deploy cables in outdoor sites that are building-adjacent
- Can reduce ongoing inspection and maintenance costs of networks, particularly safety-critical ones which have to be checked more regularly
- Can utilise the advanced security provided by network slicing to remove the need for separate, isolated networks in some circumstances
- Can lower the incremental costs of adding new functionality and use cases compared to a wired network due to reduced equipment and deployment requirements.
- Can facilitate the removal of multiple other networks: Wi-Fi, wired, Bluetooth, LoRa Wan etc.
To realize these advantages, the factory must integrate 5G with other technologies like IoT, AI, and robotics. The infrastructure must support high-speed, low-latency connectivity, and there should be a commitment to digital transformation to ensure the whole business is aware of how to exploit the advantages it provides. Key considerations include vendor selection, compatibility with existing systems, scalability, and support services. It's crucial to choose vendors with a proven track record in 5G deployments. Timescales can vary widely but for a strong case initial benefits might be seen within 6-12 months, with full realization of savings and efficiencies typically occurring over 2-3 years as the technology is deployed across more use cases.
Investment can be approached through CapEx for self-owned infrastructure and equipment or OpEx for managed services. This choice depends on your company’s financial strategy and preferences, with money often available through Government incentives for digital transformation, especially for SME organisations.
Benefits
Creating a “Connected Factory” through the deployment of 5G and other advanced wireless solutions can offer numerous benefits. A unified 5G network can replace multiple existing networks such as Wi-Fi, Bluetooth, mobile phones, and IoT, simplifying network management and reducing the risk of security breaches by minimizing potential entry points for cyber threats. Additionally, 5G's licensed spectrum is less congested compared to Wi-Fi, providing more reliable and secure connectivity. This newer technology can also be more easily “sliced” into separate, secure networks that can be safely shared by different stakeholder groups and used for different purposes.
From an operational perspective, 5G offers significant flexibility and efficiency. In large factories, Wi-Fi requires numerous access points to ensure comprehensive coverage, whereas 5G can achieve the same with considerably fewer antennas. This not only reduces infrastructure costs but also simplifies maintenance. The high-speed, low-latency nature of 5G means that new use cases, such as real-time monitoring and automation, can be implemented without negatively impacting the existing network. Furthermore, the ability to deploy a private 5G network allows manufacturers to tailor connectivity solutions to their specific needs, ensuring optimal performance and reliability. Overall, the adoption of 5G and advanced wireless solutions can lead to a more streamlined, secure, and efficient manufacturing environment.
Lessons Learnt
Here are some recommendations for deploying a 5G network in a factory or manufacturing environment:
- DO start by creating a proof-of-concept deployment that is separate to existing IT networks and infrastructure. This will help demonstrate value and tangible results before having to go through a full IT service transition and operationalisation process. DON’T ignore IT though, bring them along for the journey!
- DO include training and documentation for end-users and support teams as part of a deployment. IT departments and the wider business may be hesitant to adopt 5G due to unfamiliarity. Providing training and highlighting the similarities between 5G and existing Wi-Fi and network systems can alleviate concerns and facilitate acceptance. Include this expense as part of the Cap-Ex plan for initial deployment.
- DON’T deploy critical use cases onto the system until you have ensured that the 5G platform is available and operational. Conduct thorough site surveys and infrastructure assessments to identify areas 5G deployment is feasible, and prioritize these locations.
DO treat 5G deployment as a series of stepping stones. You won’t be able to get the full value of a connected factory in one go so don’t try to start with an over-complicated delivery plan. Deploy with an initial high-value business case that addresses immediate needs, then start to layer additional use cases and applications on top.
- DO ensure robust security measures are in place. 5G networks introduce both improved security and potential new challenges so utilize encryption, network segmentation, and regular security audits to safeguard the network and deploy robust security protocols to protect sensitive data and prevent unauthorized access.
- DO leverage network slicing for different user groups. This is a feature of 5G that allows for the creation of virtual networks tailored to specific user groups or applications, ensure optimal performance and resource allocation so identify key user groups and their requirements and configure network slices accordingly.
- DO monitor and optimize network performance continuously. This is essential to maintain high network performance and promptly address any issues that arise and should include implementing monitoring tools and benchmarks that are regularly reviewed and acted upon.
- DON’T isolate the 5G team from other departments. Successful deployment requires collaboration across various departments, including IT, operations, and management. Foster a culture of collaboration by involving key stakeholders in planning and decision-making processes. Regularly update all relevant parties on progress and challenges.
If you’re ready to embark on a connectivity project, we can point you to the suppliers with expertise in your sector.